Information and Media Outreach Cell
IIT Kanpur
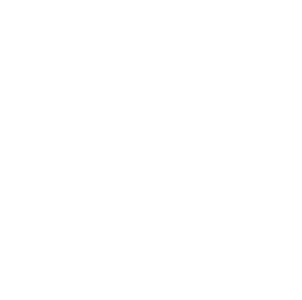
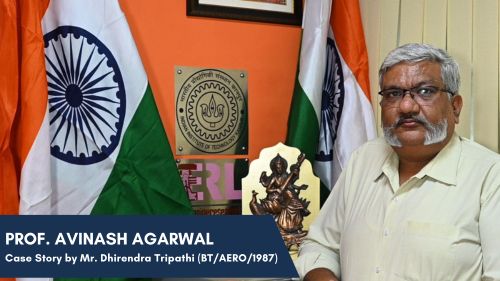
Prof. Avinash Agarwal - Research Musings
16 Feb, 2024 | Research & Innovation
This is the story of path breaking research that has developed a new cutting edge technology. It has done so by pursuing the core research work with great rigour, creativity and persistence, adopting a first principles approach to theoretical and experiment design aspects of the research.
Source: https://demo.gyanyogi.com/aarcs.html
Travel broadens the mind
Prof Avinash visited the Technical University (TU) of Vienna in 2004. That is when he got interested in Laser Ignition, which he witnessed in his host Prof. Ernst Wintner’s lab at the Photonics Institute, Vienna. Prof. Wintner is a Physicist. He has made a sustained effort over more than a decade to develop technology for using a laser as an option for ignition. He further developed the technology to use laser ignition in large Mega-Watt size engines. These engines have a rather low rpm in the range of 500-800 rpm. He collaborated with Jenbacher, a company manufacturing engines with more than 10 inches bore. These are normally 16-cylinder engines. He successfully demonstrated laser ignition in one of the cylinders in collaboration with Dr Gunther Herdin of Jenbacher. Jenbacher was later acquired by GE.
Recognizing the challenge
Prof Wintner's cherished objective was a demonstration of laser ignition for a much smaller automotive size engine, with a cylinder volume of 500 to 700 cc and a speed of 1500-3000 rpm. He was however feeling constrained since he was a physicist. He realized he needed to collaborate with an engine expert, who would take an active interest and take ownership of the challenge of laser ignition in smaller engines. A key challenge was the cylinder head of a smaller engine. The cylinder head has space constraints, so designing a laser spark plug that was small enough was important. In addition, the alignment of the laser beam with the laser spark plug was critical. The synchronisation of engine sensors with the laser at a high speed was another important challenge. Prof Wintner motivated Prof Avinash to take up these challenges when he became interested in laser ignition in 2004.
The strength of teamwork between student and guide
Designing and fabricating a laser-ignited CNG/Hydrogen fuel engine of automotive size was the specific area where the interests merged. The collaboration led to a six month long visit of Dhananjay Kumar Srivastava, who was working with Prof Avinash as project staff, to TU Vienna in 2005. Dhananjay had, at the time, just completed his M Tech in Materials Science under the supervision of Prof Avinash. Dhananjay was an able student and a quick learner. He had demonstrated his diverse abilities when he designed an engine simulator for wear testing of the piston rings and liners during his Masters’ thesis project. He published a journal paper based on the thesis. He had worked further in the field and developed an innovative experimental setup, right from design to fabrication. He did it from scratch in Prof Avinash's laboratory using the limited resources available at the time. Dhananjay then performed the wear experiments in the Engine Research Laboratory (ERL), followed by testing and characterising of worn-out surfaces using the central facilities of the institute. He got exciting results, which were published in the Materials and Design journal. He stayed in Prof Wintner’s laboratory for six months and successfully created plasma in a constant volume combustion chamber sometimes referred to as a combustion bomb. He conducted a few experiments on laser ignition of methane and air mixtures. He collected enough data to publish two papers in reputed international journals. This excited him enough to pursue his PhD at IIT Kanpur and take up laser ignition as the area for his doctoral research.
A great team is just the starting point
However, one of the immediate challenges was that there was no experimental infrastructure available for undertaking laser ignition research. This challenge had to be met. The need was to sufficiently match and then go beyond the setup at Prof Wintner's laboratory in TU Vienna. This involved building a combustion bomb based experimental setup. We could then learn more about laser ignition, and undertake the challenge of building a laser ignition based engine prototype. This was a complex challenge, starting with getting sufficient funding for setting up the infrastructure. A project proposal for exploring laser ignition was prepare which was accepted and funded by Department of Science and Technology (DST). Dhananjay designed the constant volume combustion chamber (CVCC) or combustion bomb as we call it using Computer-aided design (CAD) software. Designing the CVCC took quite some time, since first Dhananjay had to get familiar with the software first and then incorporate all the machining tolerances during the design stage. The choice of the material was very important for structural integrity and ultimately safety. The material had to be able to withstand very high temperatures and pressures. That too at a very high rate of increase of pressure. Any structural failure could have led to a catastrophic accident. Therefore, reasonable factors of safety were assumed for each component during the design stage. There was a flip side though as the design had to be done ensuring that the system did not become too heavy and bulky due to very high factors of safety. The first principles approach of IITK got to work here and more rigorous stress analysis was done for various materials. Finally SS-314 emerged as the material of choice to manufacture the CVCC. The central workshop, at IIT Kanpur, started to manufacture the parts of the combustion bomb, one at a time.
Slow take off
The manufacturing of the CVCC could begin once an SS-314 round billet weighing 125 kg was procured from Steel Authority of India (SAIL). We knew we were charting a new terrain as it tool SAIL some time to produce the billet as per the specifications. The machining of the billet was a new challenge for IITK’s Central Workshop as well. There was a waiting period of nearly two months since this was not routine work but Dhananjay patiently and skillfully guided the operation.
Slow and steady progress
The machining work was challenging for the Central Workshop at IIT Kanpur not only because it was not a routine request. SS-314 is a hard material to machine which takes a toll on the cutting tools. A lot of money was spent on cutting tools. It took about a year to machine the combustion bomb and then the system assembly started. One of the major challenges was to ensure the chamber was leak-proof. No fuel-air mixture could escape when the combustion bomb was filled under pressure up to 10 bar. Several gaskets were tested without success during the dry runs. Finally, we devised a metallic mesh gasket which could perform the role of the main gasket at high pressure and temperature conditions. Teflon gaskets sealed the leakage from the optical windows, these were easier to seal since they were smaller. In the meantime, several instruments had been procured from different parts of the world to be deployed in various sub-systems. These were integrated with the CVCC over the next six months. These sub-systems posed their own challenges. For example it was required develop a sub-system to release the fuel gas and air at different partial pressures in the CVCC to enable an experiment to have a predetermined mixture strength in the CVCC.
Integrating the CVCC with the laser
The CVCC had four optical windows for laser propagation and imaging. The laser and the optics were optimized to generate plasma in the ambient air. Plasma is the fourth state of matter consisting of highly ionized gases at a very high temperature. A pressure transducer was installed to keep a tab on the heat release rate inside the CVCC using a high-speed combustion data acquisition system. Though all these sub-systems were tested in isolation the greater challenge task was to make them talk to each other and to synchronise them. This was critical for the experiment’s success. First synchronisation was established between the high-speed Charged-Coupled Device (CCD) Camera, the laser and the in-cylinder pressure data acquisition system. A signal from the CCD camera was used to trigger the laser and pressure acquisition system.
While sculpting reality, experience is very useful
Setting up the laser ignition experiment could now begin. This would be the first such set up on Indian soil. Dhananjay had gained experience in key aspects such as laser handling, sub-system synchronisation, laser beam and plasma characterisation at TU Vienna. This helped him setting up laser ignited CVCC experiment at IITK. Close to two years since we began the journey we started initial experimentation by generating plasma. The plasma had a temperature of one million degrees and generated a shock wave of 1000 bar pressure inside the CVCC. It had been an enjoyable journey full of determination regularly overcoming challenges as a team.
The importance of a supportive technology ecosystem in innovation
There was elation when laser plasma was created for the first time. However there was a lot more to be done. In a CVCC, the laser had to fire only once, on our command. So it was important to operate the laser in an “external mode”. For this a circuit had to be designed. It was decided to take the help of some enthusiastic undergraduate (UG) students of the electronics club at IIT Kanpur. Dhananjay again demonstrated his skill at working with people and he motivated these UG students, who loved hands on work, to solve some challenging problems. Dhananjay was very excited when combustion was triggered in the CVCC for the first time. He came running to my office to show me the video that was captured of combustion using CNG-air mixtures. The results were very similar to those in TU Vienna, so he had successfully recreated key aspects of the CVCC experimental set-up at TU Vienna. This was done in just a little over two years which was a remarkable achievement. Over the next year numerous experiments were performed. Fundamental experimental data was obtained for laser ignition of natural gas/ hydrogen-air mixtures. Crucially the team had gained a lot of confidence. This was extremely important for initiating the actual engine experiments.
Developing an engine prototype
Development of an engine prototype for laser ignition could now start. The experimental engine had already been procured and set up in parallel while we performed combustion bomb experiments. Along with the engine, dynamometers and several other instruments for engine experiments had been obtained. The main challenge was to make the laser work in sync with the engine. The laser pulse had to be fired at a fixed point in the engine cycle, but the engine rpm varied constantly and coordinating the laser pulse required further engineering. We now knew what was required and we developed a strategy to control the laser in an external mode. The actual synchronisation required the development of electronic circuits. Once again enthusiastic UG students of the electronics club were very eager contributors. The students were enthusiastic because building the solution offered a relatively rare chance for them to use their outstanding hands-on engineering skills. We should nurture this talent in the UG students and offer them more challenges that they will undertake eagerly. We now had the laser synchronised with the engine. The design, fabrication and testing of the laser spark plug was the next challenge we faced.
Where there was smoke there was plasma!
Designing the laser spark plug was a multidisciplinary challenge. The design involved getting many things right for the laser spark plug to perform as desired. The location within the combustion chamber where combustion had to be triggered had to be identified. Laser devices are available with a fixed frequency and we needed variable frequency synchronized at all times with the engine. The location and timing of the ignition had to be controlled within very small tolerances. For example the ignition had to be controlled down to less than a micro second, close to a nano second. These challenges were met by building a quality team to work on each issue with dogged persistence in carrying out iterations. Ultimately this effort paid off and a laser spark plug was designed and fabricated.
The laser spark plug now had to be integrated with the engine. It was decided to fit the laser spark plug that we had designed on the cylinder head keeping the cylinder head detached from the rest of the engine. The idea was to see if plasma could be created in the space below the cylinder head when the laser pulse passed through the spark plug. This did not happen. Even after many trials. Persistence though has its rewards and Dhananjay. While pondering the issue Dhananjay puffed cigarette smoke towards the space below the cylinder head. And bingo!! ...plasma was generated.
Since the combustion chamber had been set up with meticulous care, the air in the combustion chamber was very clean. It lacked the impurities that speed up the creation of the plasma. In a normal internal combustion engine situation impurities abound. The introduction of smoke brought in the crucial impurities which triggered the ionization and plasma was created.
The experiment was now successful, albeit at the cost to an embarrassed Dhananjay that his project guide now knew he smoked. Creating smoke like conditions in the cylinder was not a big challenge because there are always burnt gases leftover in the cylinder from the previous engine cycle. We fined tuned the laser further and finally assembled the engine to test running it using laser ignition.
Need for persistence and then some more persistence
The excitement of entering the final phase of the experiment to run the engine was high but slowly the enthusiasm ebbed away. The engine just would not fire! Since we were doing pioneering work it turned out that many refinements were required. The team patiently undertook troubleshooting day in and day out. Instead of moving forward with long strides were were now inching towards our goal. It took months of troubleshooting with different components and the hard work of the students and staff of the ERL. Dhananjay was very determined and loves working in the lab on Sundays. On Sundays he could concentrate peacefully on some of the technical issues with an undisturbed mind. On one such Sunday afternoon at around 2 PM, while I was having my lunch, Dhananjay called me to reach the lab as soon as possible. I rushed to the lab immediately, and then Dhananjay told me he the engine had fired successfully, using laser ignition, for the first time. When Prof Avinash saw the demonstration, he was mightily pleased to see the breakthrough happening in the ERL. It had come after a sustained effort to understand the fundamentals of a complicated technology. And then develop a possible product for the future based on that technology. Here is an image from that afternoon. It is worth over a thousand words!
Reaping the rewards
Over the next two years, a host of experiments were performed using methane and later on hydrogen and methane-hydrogen mixtures. By this time, the next student, Rajesh Kumar Prasad, had joined the effort. When Prof Wintner was informed about the success in developing a working laser-ignited automotive size engine in based thanks to his motivation, he was very happy and proud of the joint effort. It had taken four to five years of sustained effort. This effort involved many technical challenges, each was resolved with great patience and perseverance. My team was unfamiliar with the laser and the electronic circuits to control the lasers. The class 4 lasers were invisible and could be extremely dangerous if not handled properly. The challenge of making all the components communicate so that they could be synchronised was an enjoyable one. That experience provided a lot of learning.
GUIDANCE FOR YOUNG RESEARCHERS
On the need for hands on work in research
One thing is very clear. Solutions to the majority of such problems cannot be found in a textbook. Nor can they be taught in a classroom. One has to do it the hard way. Struggle, make mistakes, analyse one’s failures and constantly keep coming up with possible solutions till finally the problem is cracked.
On the student guide relationship and being emotional
In addition to understanding the theory well, one has to apply the knowledge and repeatedly innovate. One has to tirelessly try out one’s ideas, learn from the experience and make more refined efforts till the goal is achieved. The guide plays a key role here as the students can undertake this journey only when they have the complete and unflinching support of the supervisor, not only for their successes but also for covering their failures and mistakes. Overall the research journey is very exciting. It is sprinkled with emotions such as frustrations due to failures, making choices that did not work out and finally succeeding and the joy of achieving the goal. At the end of the day, all researchers are human beings and have emotions which give value and meaning to their lives.
Interdisciplinary challenges need a brave outlook
The underlying cause for the effort being so challenging was that this kind of research problem is extremely interdisciplinary in nature, and there is a great deal of uncertainty about whether it will ultimately be successful. It is human nature to avoid getting out of the comfort zone and instead choose to, as far as possible, limit oneself to the area in which one is trained. Given that uncertainty, researchers often prefer to work on problems that are not interdisciplinary, and the chances of success are much higher. Convincing the funding agencies to provide resources for risky problems is also difficult. Earlier expert committees were very conservative, and convincing them about the risks and new ideas involved was not easy. Off late, though, this is changing, which is very good news for ambitious researchers.
On dealing with failures encountered in the research journey
One has to understand 'dar ke aage jeet hai…' (beyond fear lies victory...). One has to overcome the fear of failure and take risks. Only then can one make exceptional achievements. Incremental research by itself will definitely not help our country, but that has been the norm in the Indian scientific community. However, this mindset is also changing slowly. Our successes in this one area of research have given us reasonable standing worldwide, and we are now known as the researchers who can take up risky problems and take them to a conclusion without getting bogged down. I have this firm conviction that every technical problem has a technical solution.
Not all problems that need to be solved are technical
Technical problems should not be left unattended because of non-technical issues, which often happen, unfortunately. Even though I was successful in performing difficult experiments in IITK, the general ambience has not been very conducive traditionally for experimentalists in IIT Kanpur, which has achieved great success thanks to its acclaimed theoreticians. Therefore it was difficult for researchers like me, who are hard-core experimentalists involved in applied research, when I was competing for resources. For IIT Kanpur to be a leading R&D institution, there should be better internal recognition of the contributions of experimentalists. Experimentalists are key to developing technologies with a high social impact which is increasingly expected by the country’s researchers with each passing day.
On sustaining one's research momentum
Many academic researchers lose steam, particularly after their initial success helps them achieve their immediate goals. Only a few researchers can sustain the research momentum for a long period. Only the inborn drive for excellence in research keeps these few researchers motivated. They continue to perform well at what they cherish most.